Resources and skills
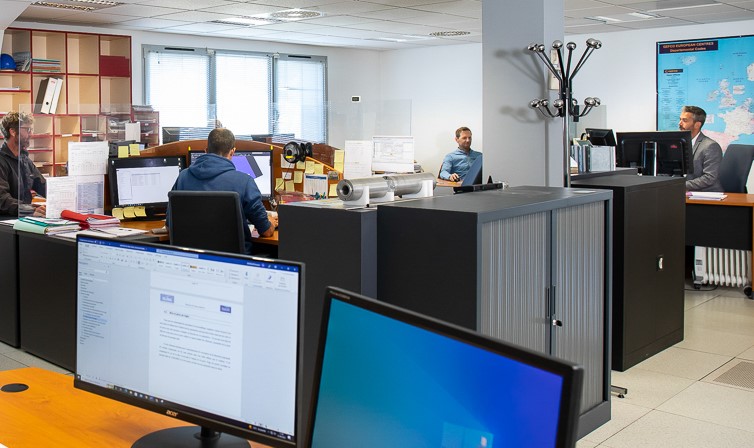
Our strengths and talents
Our single production site covers 10,000 m² and brings together all the skills and expertise necessary to meet your needs.
Our workforce of more than 50 employees is organized by product lines in order to provide you with the necessary flexibility and reactivity.
- Complex projects: Supply and installation of secure rooms, EMC & RF anechoic chambers according to specific design, turnkey projects integrating third party equipment.
- Standard projects: Supply and installation of EMC, RF and cyber products from the catalogue. Minor adaptations can be made if reconsideration of the design is not required.
- Simple products: Supply of equipment requiring no development, available off the shelf.
This organization generates a high level of technical support on the part of all our departments, coupled with individually tailored follow-up for our customers (project reviews can be performed without difficulty at any time).
Our multifaceted skill sets, together with our extensive international experience, allow us to get to grips with projects of all types and demonstrate the extent of our expertise. Thanks to our highly qualified technical staff, we offer high-value-added engineering and production expertise.
In addition, being part of Cegelec Défense, a Vinci Energies group, provides financial stability in line with the group’s results.
The ISO 17025 certification which we were awarded in 2017 for our chamber and shielded room measurements represents a guarantee of the quality of our services and confirms the fine-tuned performance levels of our installations.
Standard and complex projects are handled by a Business Manager and a Project Manager.
The Business Manager will be the main contact for the following stages:
– Helping to define the need, contributing and sharing our industrial experience
– Qualification work with the client
– Preparing the costing and drawing up the offer in line with the building’s constraints, the budget and the client’s schedule
– Negotiation and acceptance of the order
– Supervision of the project until the end of the service
The project manager, your direct contact at every stage:
– Sending the drawings for the project and taking into account any changes to be made
– Management of supplies
– Follow-up during the manufacturing process
– Supervision of logistics, stages prior to the site
– Integration of test instrumentation for turnkey projects
– Management of any subcontractors, link with related trades for interfaces
As simple products do not require on-site intervention, they are handled by the project managers from the definition of the need to delivery. They are supported internally by the technical referents.
– R&D Department which monitors standards and looks for innovative solutions
– Ensures responsiveness to changes in regulations and standards
– Custom designs to meet specific requirements
– Consultation with the customer in order to define the location of the various elements forming the test facility: door, feed-throughs, etc.
– Preparation of technical drawings and production plans
– Coordination with the Project Manager
– Production of special panels and feed-throughs
– Manufacture of high-performance doors
– Manufacture of shielded boxes
– Preparation of components
– Control of the production cycle: impregnation, painting, drying, etc.
– Adaptability in terms of production volumes and reactivity
Support for your test resources during:
– The operation of your installation: maintenance, modifications, upgrades, etc.
– Potential movements of equipment: disassembly, relocation, evacuation, reprocessing, etc.
– Factory acceptance tests (FAT) thanks to our coaxial line as well as our anechoic and reverberation chambers. Site acceptance tests (SAT) following installation
– Performed by our Siepel Measurements department whose personnel and associated equipment have ISO 17025 accreditation
– In accordance with applicable standards (shielding efficiency, VSWR site measurements, field uniformity, etc.)
– A supervisor directs the on-site Siepel installation team and/or the local workforce
– Installation activities performed worldwide
– Management of associated work packages provided by partners and the interfaces with them
– Fully comprehensive insurance contract during installation
– Packaging and wrapping appropriate for the selected mode of transport
– Shipment throughout the world
– At the administrative level: choice of the mode of transport, preparation of export documentation, finalization of contracts with forwarding agents and carriers, etc.
– All the products manufactured at our factory are inspected prior to shipment
– Monitoring of the procedures defined in our quality management system, which is based on ISO 9001